On 22rd and 23rd October 2015, fifteen nuclear professionals participated in a Technical Visit to three AREVA facilities in France. This event was jointly organised by the NI London Branch and NI South East Branch.
While twelve of us met up at Gatwick Airport and caught a flight, three more NI delegates who were already in France hired a car and joined us at the facility. We booked into our hotel in Chalon (around 120km north of Lyon), hired a coach to travel between the facilities, and spent the evening enjoying the local cuisine. The entire first day was taken up by a technical visit to the Le Creusot facility with two more tours of Chalon St Marcel and Chalon Cetic taking place on the second day before a flight home on which we all caught up on some much needed rest.
Le Creusot
Our first visit of the trip was to Le Creusot forge which is located around 40km west of Chalon. Once the coach driver dropped us off at the right location (it took 15 minutes for a journey that ended up taking us from one side of a gate to the other) we were all very surprised to see that the factory is right in the middle of town. Our guide for the trip was Lionel Sibille, a very friendly sales manager.
Le Creusot forge specialises in the supply of big forgings and castings for the nuclear market. To date they have supplied over 2,800 parts for over 100 nuclear plants worldwide. They are one of the very few forges in the world capable of making the sophisticated parts necessary for the manufacture of the primary components for the nuclear island. The main type of components produced at Creusot forge are reactor pressure vessels, steam generators, pressurisers, primary pumps and primary piping (hot and cold legs), which are then transferred down the road to Chalon St Marcel to be assembled. They are also now looking to diversify into producing spent fuel transfer casks, and large components for wind energy, petrochemicals and shipping.
The region has a rich history in steel works with the first smelting operations occurring at Le Creusot in 1782. Forgings for the nuclear industry started in the late 1950s with the commissioning of a 7,500 tonne hydraulic press and the launch of the French commercial reactor program. Today, the forging shop has two hydraulic presses, one 11,300 tonnes and the original 7,500 tonnes press which was renovated in 2008. The annual output is up to 50,000 tonnes and they are able to produce components up to 8m high, 450mm thick and 150 tonnes in weight.
The steel for the forgings arrives in the form of ingots weighing around 260 tonnes, on a rail track from the melting shop, at temperatures over 600° C. Once on site the ingots are re-heated in gas furnaces capable of bringing parts up to forging temperature (> 1200° C) within a few hours. Amazingly when we stood right outside these furnaces no waste heat could be felt; in fact the factory was very cold and needs to be heated in the winter to ensure that the I&C equipment works. The heated ingots are then forged (shaped) into the desired shape using the large hydraulic presses, which have forging powers around 90 MN and a 200 tonne manipulator which has a precision of +/- 0.25°.
Once produced the forgings are cooled using water and air quenching. Unfortunately during our visit no forgings were being produced as the hydraulic press was under maintenance (the target is for the press to be operational for four hours every day), however we were able to see a steam generator sleeve which had been produced that morning, and which was still glowing hot.
When the forgings have cooled they are moved to the machining factory next door which has over 50 machine tools for precision machining to very close tolerances and non-destructive testing. At the machining factory we were lucky enough to see a large number of spent fuel transfer tasks, steam generator sleeves for the existing French nuclear fleet, and even a Hinkley Point C hot leg!
The completed forgings are then placed back on the rail track to Chalon St Marcel for the next part of their adventure….
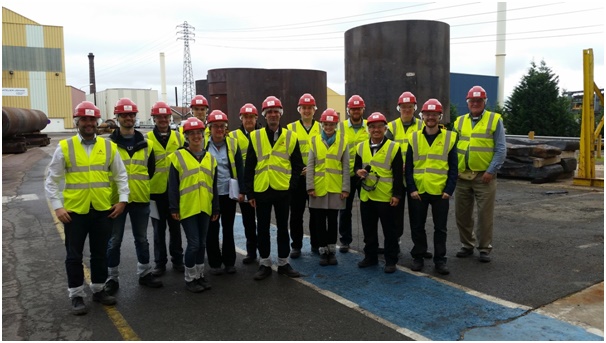
Figure 1: Group photo taken outside of Le Creusot facilities (photos are not allowed inside)
Chalon St.Marcel
On the second day of the visit, we visited Chalon St Marcel for the morning session. It felt like it was located in a reasonably large business park with Chalon Cetic, which we were to visit next in the afternoon, also forming part of this business park.
We were welcomed by Martine Vaudon, communication officer at Chalon St Marcel. Before the site tour, she gave us a presentation on the background and history of Chalon St Marcel and how the process is linked with other AREVA facilities like Le Creusot.
In terms of the process, Figure 2 shows the sequence of work flow in producing key primary circuit components of a nuclear power station such as a steam generator from start to finish. The sequence starts with steelwork being delivered to Le Creusot for forging and machining. These finished parts are then handed over to Chalon St Marcel facilities for assembling. Here, the welding, heat treatment, and quality checks play a big part in achieving the final products. They are then shipped to nuclear power stations where they will be installed. Last but not least, Chalon Cetic (Chalon Services in this figure) is the facility that holds a mock-up version of primary circuit components including reactor and fuel pools where operation personnel can come and practise a trial run before carrying out actual operations on site.
Since Chalon St Marcel was first in commission (in 1975), 671 key components have been delivered from it (almost half of which were steam generators). At present, there are 50 orders for steam generators and one order for a replacement closure head. Some of these orders are for EPR projects such as OL3 (Finland), FA3 (France), TS1 and TS2 (China), as well as existing 900-MW and 1,300-MW plants in France and South Africa.
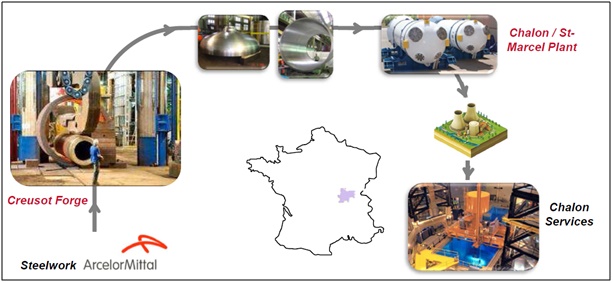
Figure 2: Cradle-to-grave process of key primary circuit components production at Areva facilities in France
Martine and her assistance, Anais Bechet, then took us on tour around site. There, we saw the assembling, welding, and heat treatment processes in action. We were also made aware of the penetration tests and inspection that needs to be done to ensure the quality of these components. All these activities take place in one big building; the separation of work process and management of different areas are cleverly managed to accommodate all these works.
Also in this building, we visited Areva’s Welding Training facility where apprentices will undergo a two year training programme to qualify after which they would be sufficiently competent to carry out 80% of welding operations.
Interesting note 1: It takes one month to complete a welding of one tube inside a reactor vessel head.
Interesting note 2: Inconel 690 Alloy is now used as the material for tubes inside steam generators, as it allows the steam generator to last the entire EPR operating life (60 years).
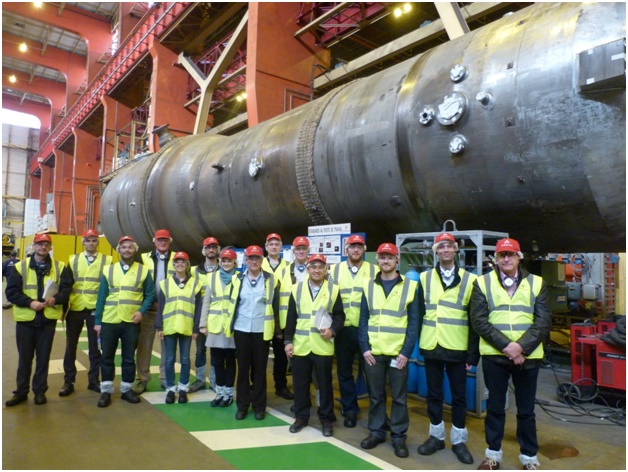
Figure 3: Our group photo with 900-MW Steam Generator during our tour led by Martine
Statistics for 900-MW Steam Generator from Figure 3:
- Cost: €30m
- Weight: 330 tonne
- Length: 20 meter
- Diameter: 5 meter
Comparison with 1300-MW Steam Generator:
- Cost: N/A (but more than €30m)
- Weight: 550 tonne
- Length: 25 meter
- Diameter: 6 meter
After our tour at Chalon St Marcel, we headed to the Commercial building (still part of the Business Park) for a lunch break prior to making our way to Chalon Cetic for our afternoon session there.
Chalon Cetic
The last visited facility was the centre CETIC (Centre d'Expérimentation et de validation des Tecnhiques d'intervention sur Chaudières nucléaires à eau sous pression – Maintenance preparation and qualification centre for pressurised water reactors’ nuclear steam supply system). As the name suggests the main aim of this facility is to create, experiment and validate the vast range of operations and interventions that a nuclear power plant requires throughout its lifetime.
In addition, other main activities of CETIC include the qualification of new intervention tools and the training of the intervention personnel. The development of new intervention methodologies allows the centre to provide its clients with tailored solutions, which translates in an improvement of the safety and the performance of their plants, while respecting their objectives of minimising costs and stop durations. AREVA itself relies on CETIC for the different phases of the intervention preparations.
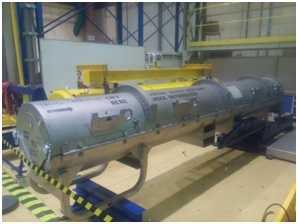
Figure 4: American Fresh Fuel Cask
|
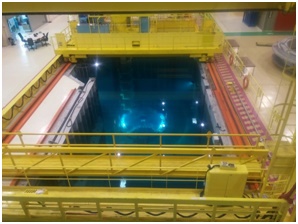
Figure 5: Fuel Loading Machine
|
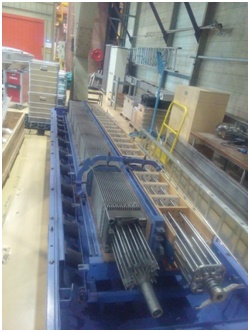
Figure 6: Fuel Assembly
|
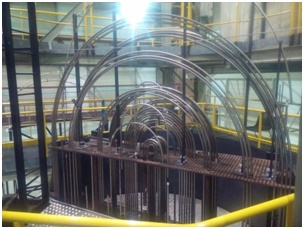
Figure 7: Steam Generators U-Tubes
|
The first stop was the description of the cask containing fresh fuel elements. The centre trains the operators with a mockup of both the American and French cask (FIGURE 4). After this the tour moved to the mockup of the fuel transfer remote manipulator, where the techniques of fuel transportation from the pressure vessel to and from the pool were explained.
The next stop was the bottom of the steam generator, where it was explained that to isolate the steam generator from the main line an operator has to go inside through a narrow man-hole and place a butterfly cap on the connection to the primary circuit. This has to be done in a very short time and operators of CETIC are able to do it in less than one minute.
The next installation was probably the biggest in the entire facility: the fuel loading machine, situated over a full size replica of an open reactor pressure vessel (FIGURE 5). The level of detail was incredible: since there was no radioactive material the pressure vessel pool was equipped with blue lights to simulate Cerenkov radiation.
The stop before the steam generators was the PWR fuel assembly (FIGURE 6), where a thorough description of the problems encountered during operations concerning assemblies and control rods was given.
Probably the most fascinating installation of the facility was the mockup of the U-tubes of a 1300 MW steam generator (FIGURE 7). It is not easy to see what is inside a steam generator because of its structure but this training facility exposed the underlying structure of the component, revealing all its engineering charm.
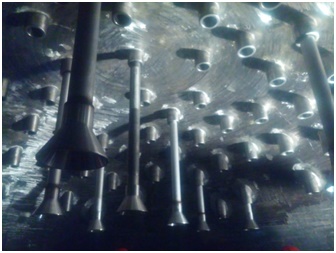
Figure 8: Vessel Head
|
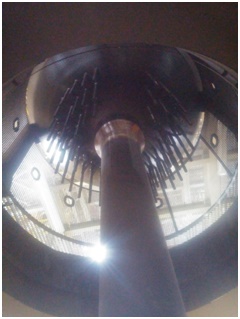
Figure 9: Bottom of the Pressuriser
|
The penultimate stop was the perfect location for some remarks on the choice of the materials for a reactor pressure vessel: it was the inside of a vessel head of a PWR (FIGURE 8). Hearing about how a thin liner of stainless steel prevented a major accident at the Davis-Besse power plant under a vessel cap was somehow fascinating, frightening and educational at the same time.
The last stop comprised a model of a pressuriser (FIGURE 9), a full hot leg connection between pressure vessel and steam generator.
At CETIC everything that is taught in university courses can be seen in full scale and full detail. The centre allows the visitor to appreciate fully the engineering complexity and/or simplicity of all the components that constitute a nuclear power plant and the safety culture that is characteristic of the nuclear industry.
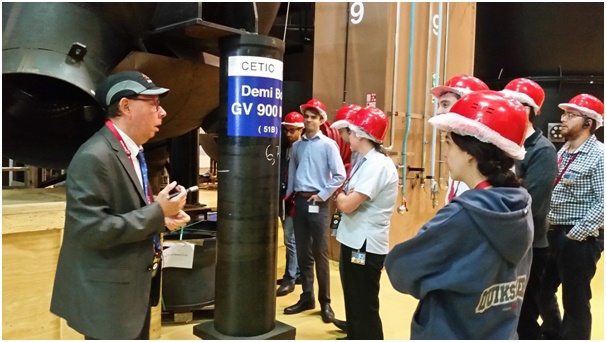
Figure 10: Lux Campbell explaining the bottom section of a steam generator to attending delegates.
On behalf of all the attending delegates, we would like to thank Lionel Sibille from Le Creusot, Martine Vaudon & Anais Bechet from Chalon St Marcel, and Pierre-Alain Lhote & Lux Campbell from Chalon Cetic for making our visit very educational and enjoyable. Your hospitality was very much appreciated.
Article prepared by:
Alex Futter (Safety Engineer from AREVA RMC)
Antonello Palazzi (Event Co-ordinator of Nuclear Institute, London branch)
Suksun Hutangkabodee (Chairperson of Nuclear Institute, South East branch)